Hydraulic proportional rotary safety solenoid valve 23871482
Details
Sealing material:Direct machining of valve body
Pressure environment:ordinary pressure
Temperature environment:one
Optional accessories:valve body
Type of drive:power-driven
Applicable medium:petroleum products
Points for attention
As a safety valve to prevent the overload of the hydraulic system the relief valve is used to prevent the overload of the system, the valve is normally closed. When the pressure in front of the valve does not exceed a preset limit, the valve is closed without oil overflow. When the pressure before the valve exceeds this limit value, the valve opens immediately, and the oil flows back to the tank or the low pressure circuit, thus preventing the overload of the hydraulic system. Usually the safety valve is used in the system with variable pump, and the overload pressure controlled by it is generally 8% to 10% higher than the working pressure of the system.
As an overflow valve, the pressure in the hydraulic system is kept constant in the quantitative pump system, and the throttle element and the load are in parallel. At this time, the valve is usually open, often overflow oil, with the different amount of oil required by the working mechanism, the amount of oil spilt from the valve is large and small, so as to adjust and balance the amount of oil entering the hydraulic system, so that the pressure in the hydraulic system remains constant. However, due to the loss of power in the overflow part, it is generally only used in the system with a low-power quantitative pump. The adjusted pressure of the relief valve should be equal to the working pressure of the system.
Remote pressure regulation: Connect the oil inlet of the remote pressure regulator to the remote control port (unloading port) of the relief valve to achieve remote pressure regulation within the set pressure range of the main relief valve.
As a unloading valve, the remote control port (unloading port) of the relief valve is connected with the fuel tank by the reversing valve, so that the oil line can be unloaded.
For multi-stage control of high and low pressure, when the reversing valve connects the remote control port (unloading port) of the relief valve and several remote pressure regulating valves, the multi-stage control of high and low pressure can be realized.
For use as a sequence valve, the top cover of the relief valve is processed into an oil drain port, and the axial hole connected to the main valve and the top cover is blocked, as shown in Figure e, and the oil spill port of the main valve is used as the secondary pressure oil outlet to be used as a sequence valve.
Unloading relief valves are generally used in pump and accumulator systems, as shown in Figure f. When the pump is working normally, it supplies oil to the accumulator. When the oil pressure in the accumulator reaches the required pressure, the relief valve is operated through the system pressure to make the pump unload, and the system will supply oil by the accumulator and work as usual; When the oil pressure of the accumulator drops, the relief valve is closed, and the oil pump continues to supply oil to the accumulator, thus ensuring the normal operation of the system.
Product specification
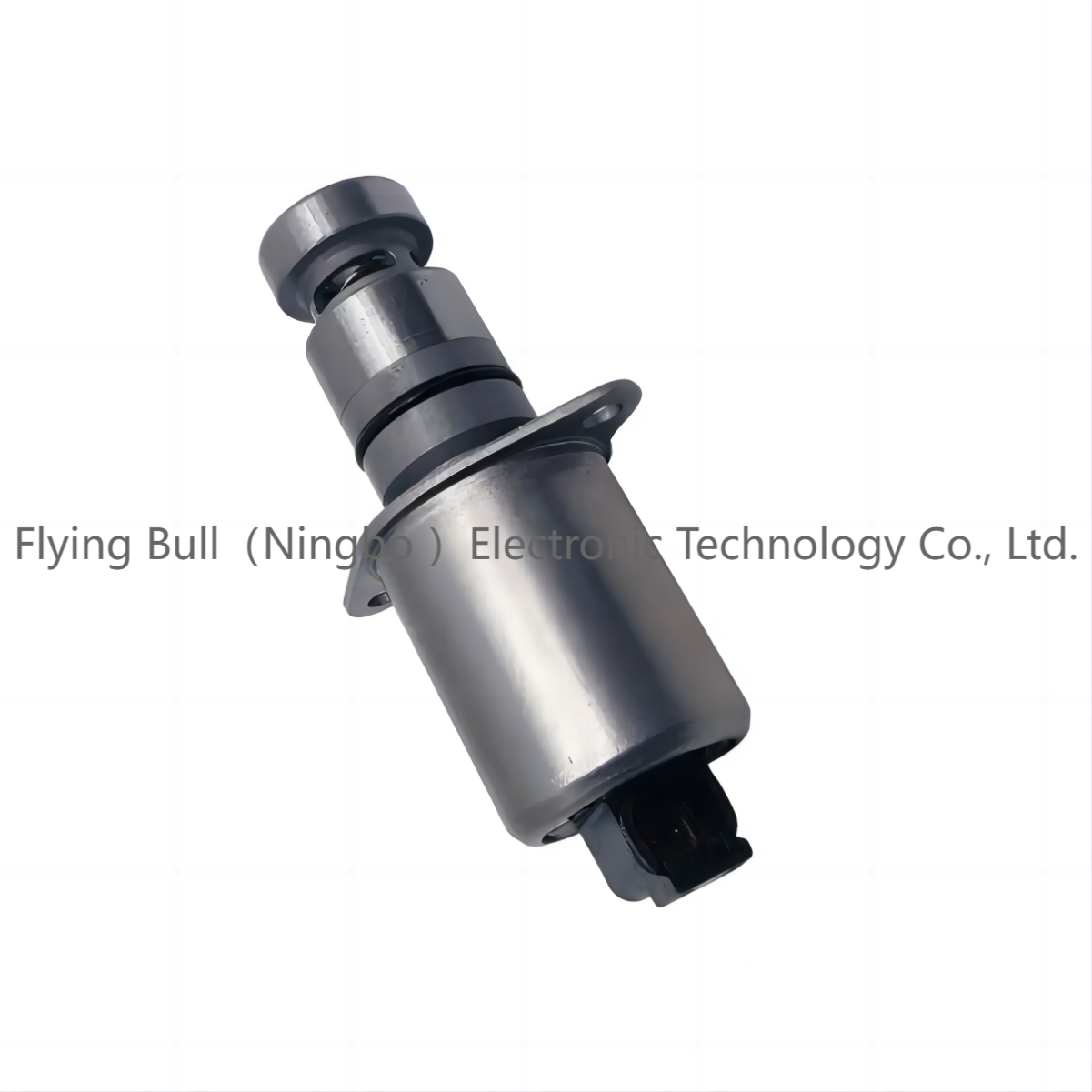
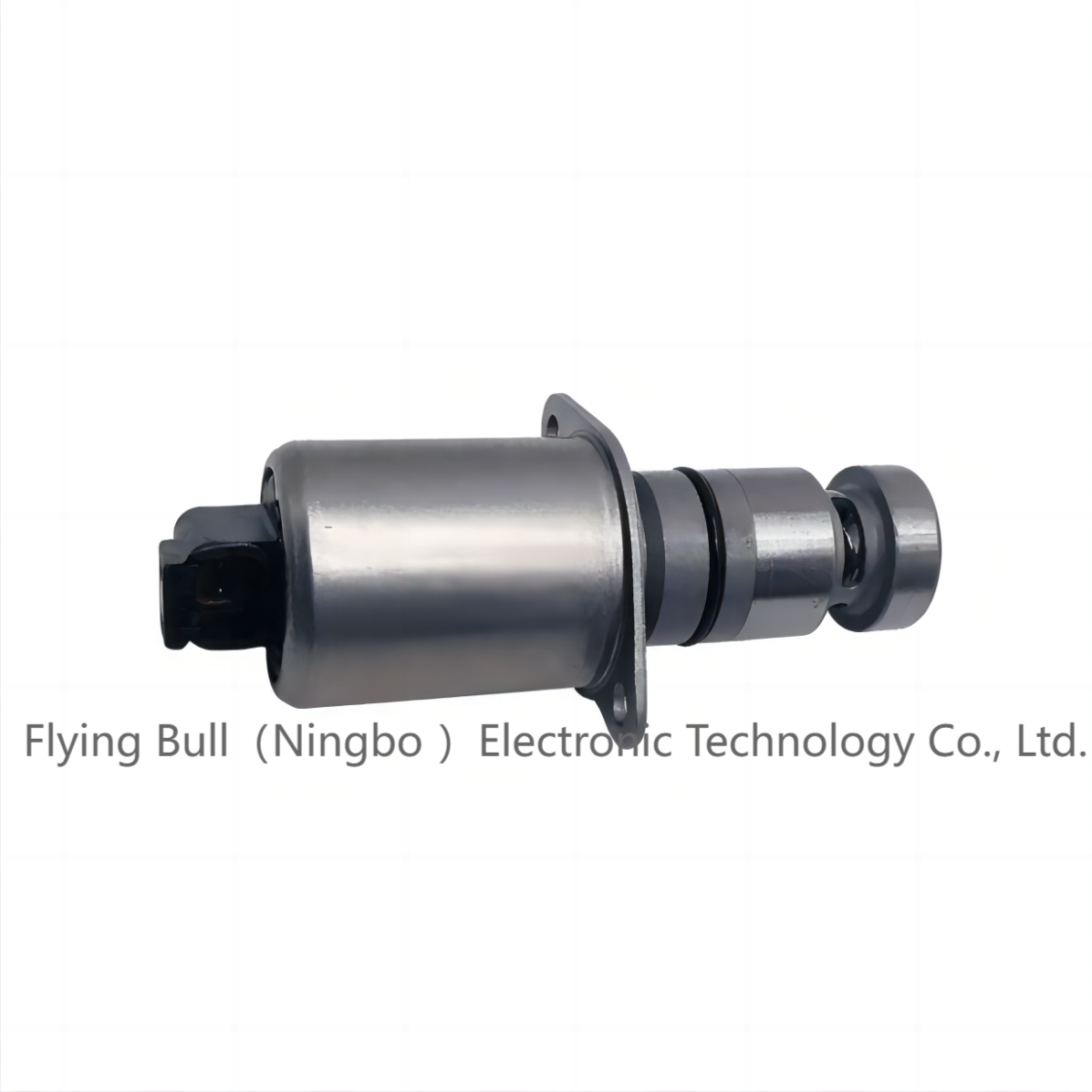
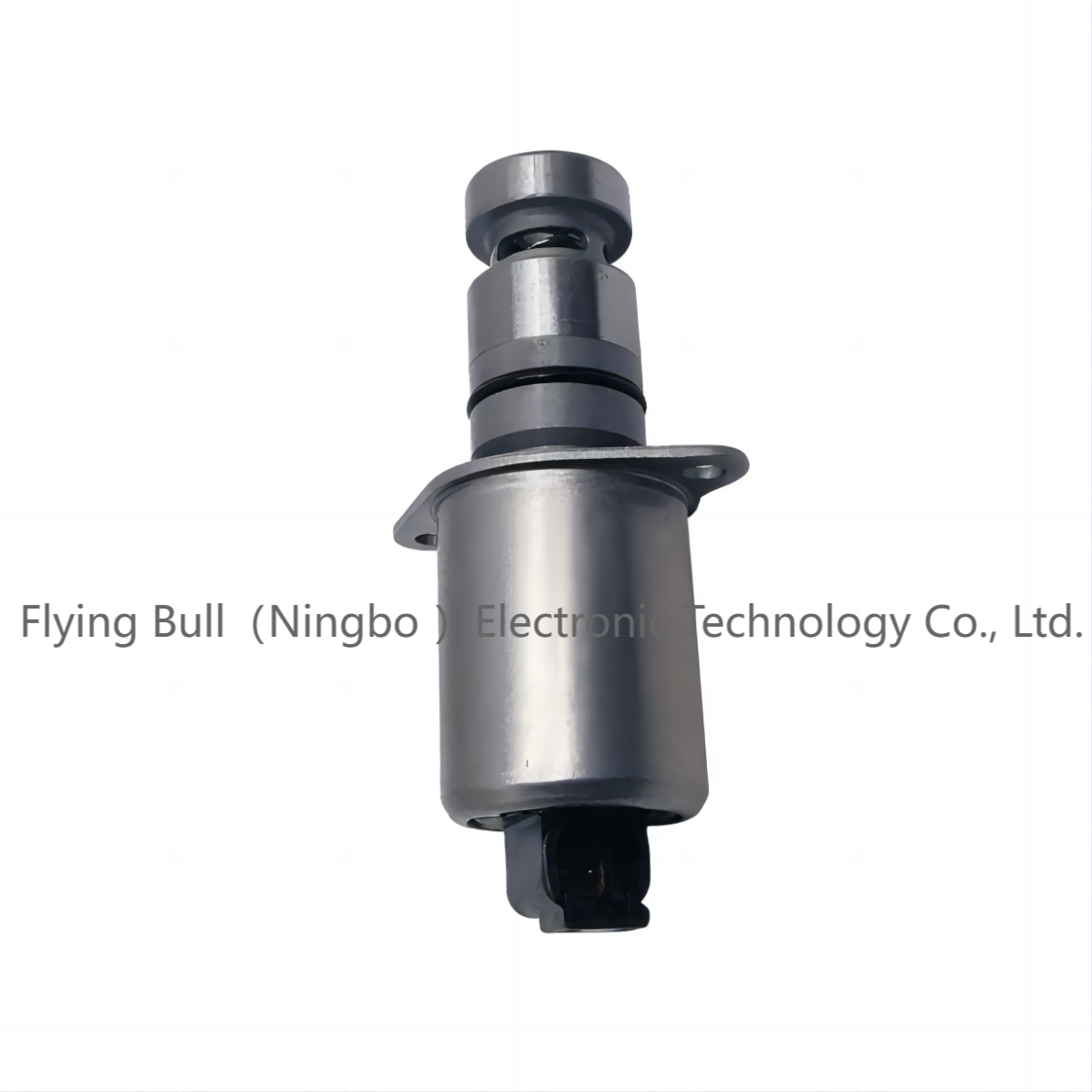
Company details

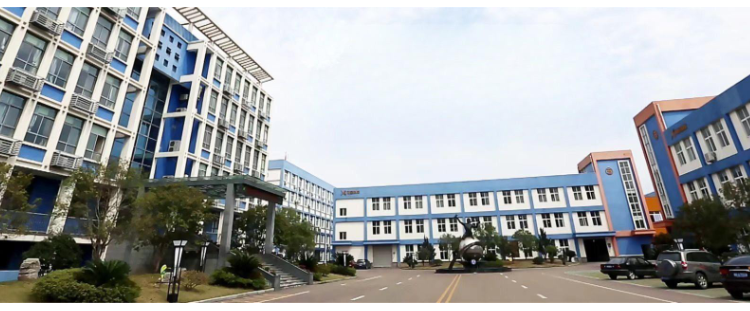
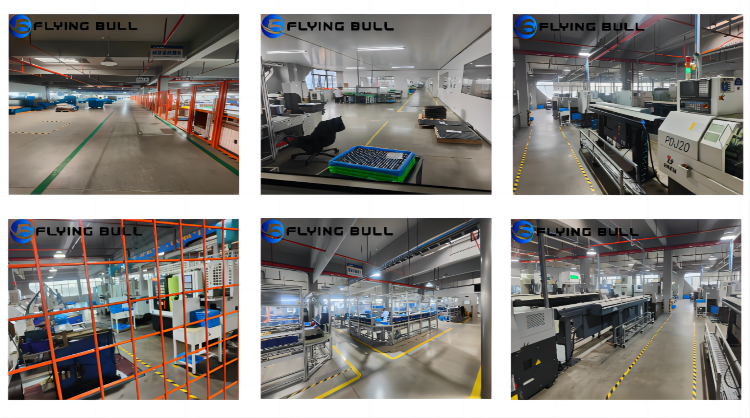
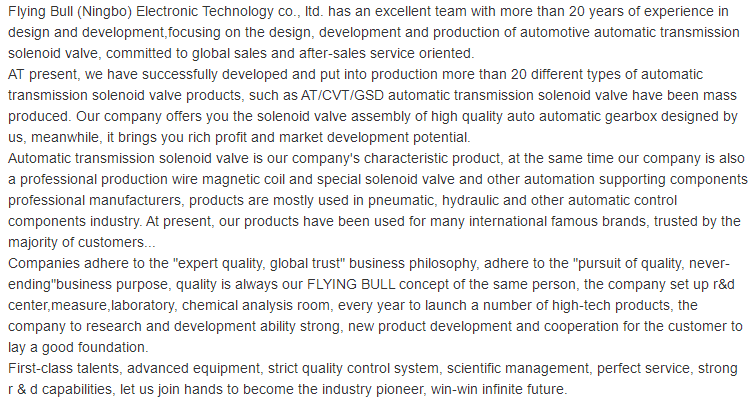
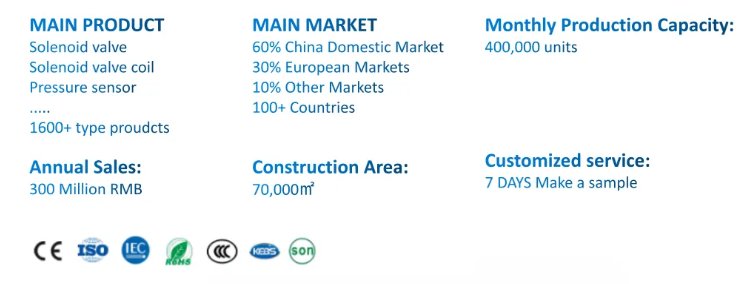
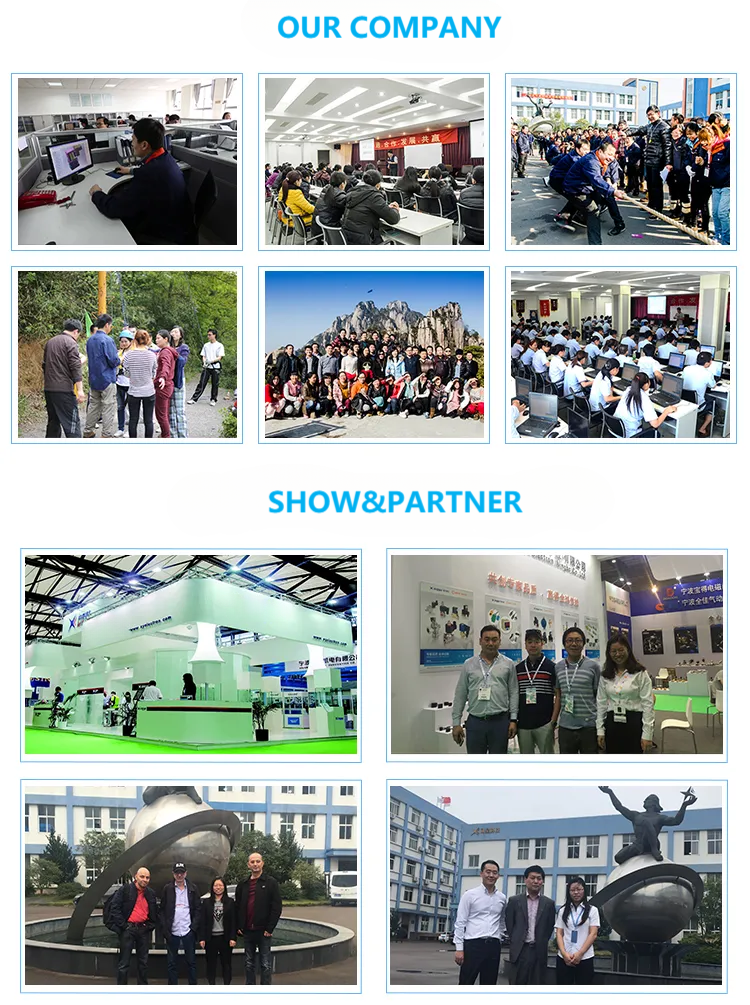
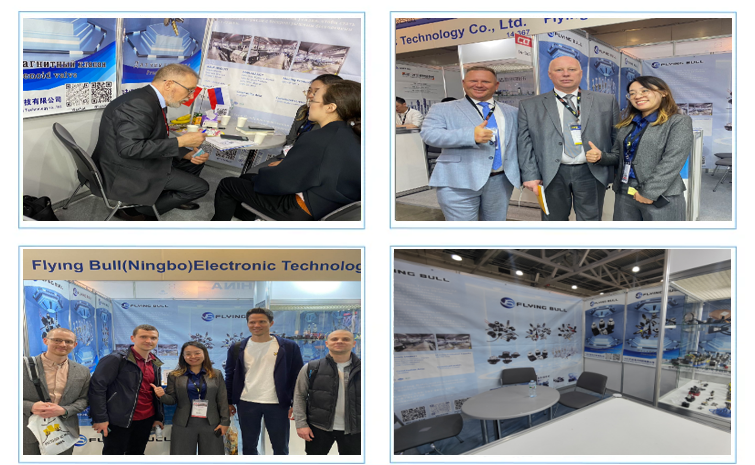
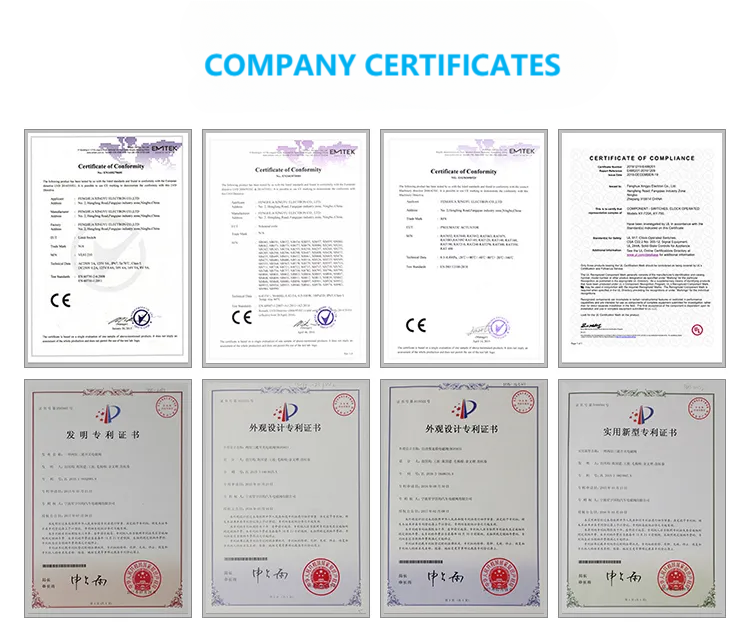
Company advantage

Transportation
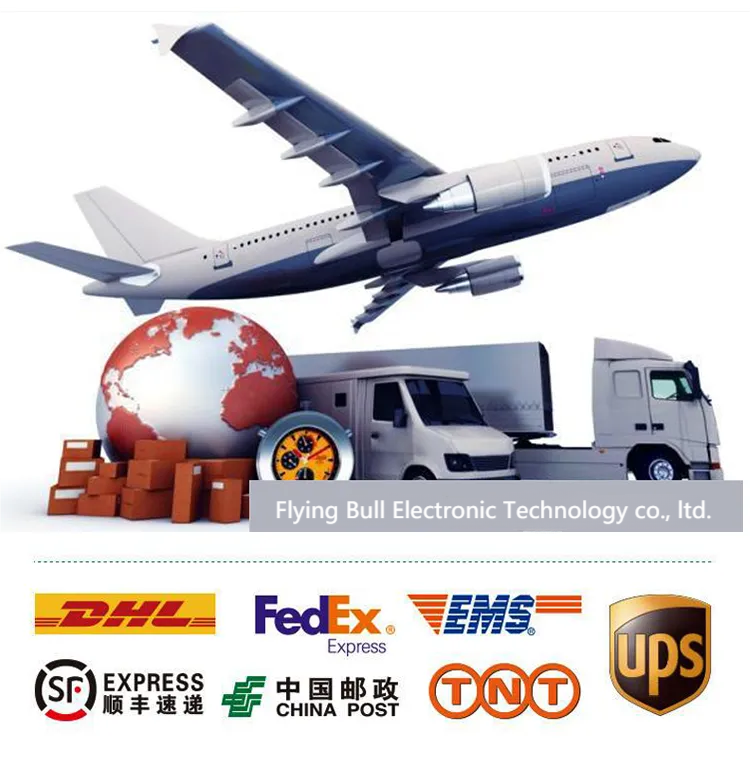
FAQ
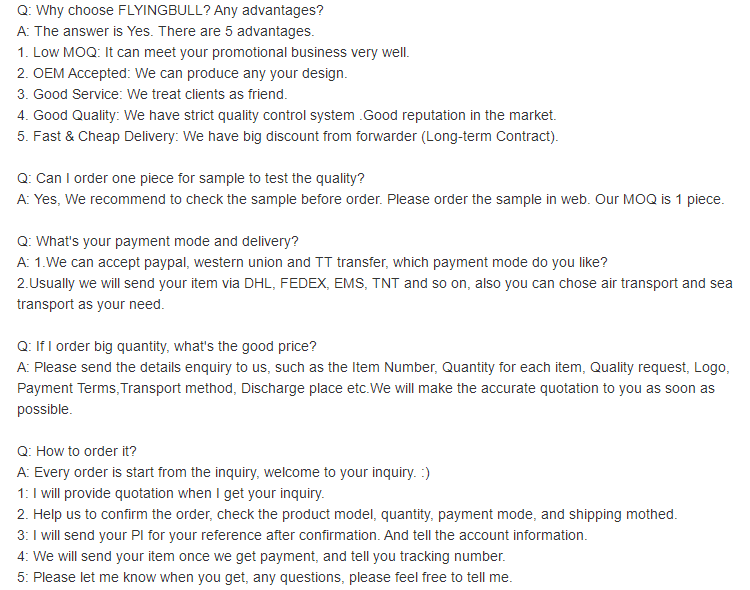