Hydraulic balance valve Excavator hydraulic cylinder valve core RVEA-LAN
Details
Dimension(L*W*H):standard
Valve type:Solenoid reversing valve
Temperature:-20~+80℃
Temperature environment:normal temperature
Applicable industries:machinery
Type of drive:electromagnetism
Applicable medium:petroleum products
Points for attention
The basic structure and working principle of the relief valve In the hydraulic transmission system, the hydraulic valve that controls the level of oil pressure is called the pressure control valve, referred to as the pressure valve. What these valves have in common is that they work on the principle that the fluid pressure acting on the spool and the spring force are balanced. First, the basic structure and working principle of the relief valve
The main function of the relief valve is to provide constant pressure or safety protection for the hydraulic system.
(A) the role and performance requirements of the relief valve
1. The role of the relief valve in the hydraulic system to maintain constant pressure is the main use of the relief valve. It is often used in throttling speed regulation systems, and flow control valves are used to adjust the flow into the system, and keep the pressure of the system basically constant. Relief valves for overload protection are generally referred to as safety valves.
2. Hydraulic system for relief valve performance requirements
(1) High pressure accuracy
(2) High sensitivity
(3) The work should be smooth and without vibration and noise
(4) When the valve is closed, the seal should be good and the leakage should be small.
(2) The structure and working principle of the relief valve
Commonly used relief valve according to its structure and basic mode of action can be reduced to direct acting type and pilot type two.
1. Direct acting relief valve The direct acting relief valve relies on the pressure oil in the system to directly act on the spool and balance the spring force to control the opening and closing action of the spool. The relief valve uses the controlled pressure as a signal to change the compression amount of the spring, thus changing the flow area of the valve port and the overflow flow rate of the system to achieve the purpose of constant pressure. When the system pressure rises, the spool rises, the flow area of the valve port increases, the overflow rate increases, and the system pressure decreases. The negative feedback effect formed by the balance and movement of the spool inside the relief valve is the basic principle of its constant pressure action, and it is also the basic working principle of all constant pressure valves.
Product specification
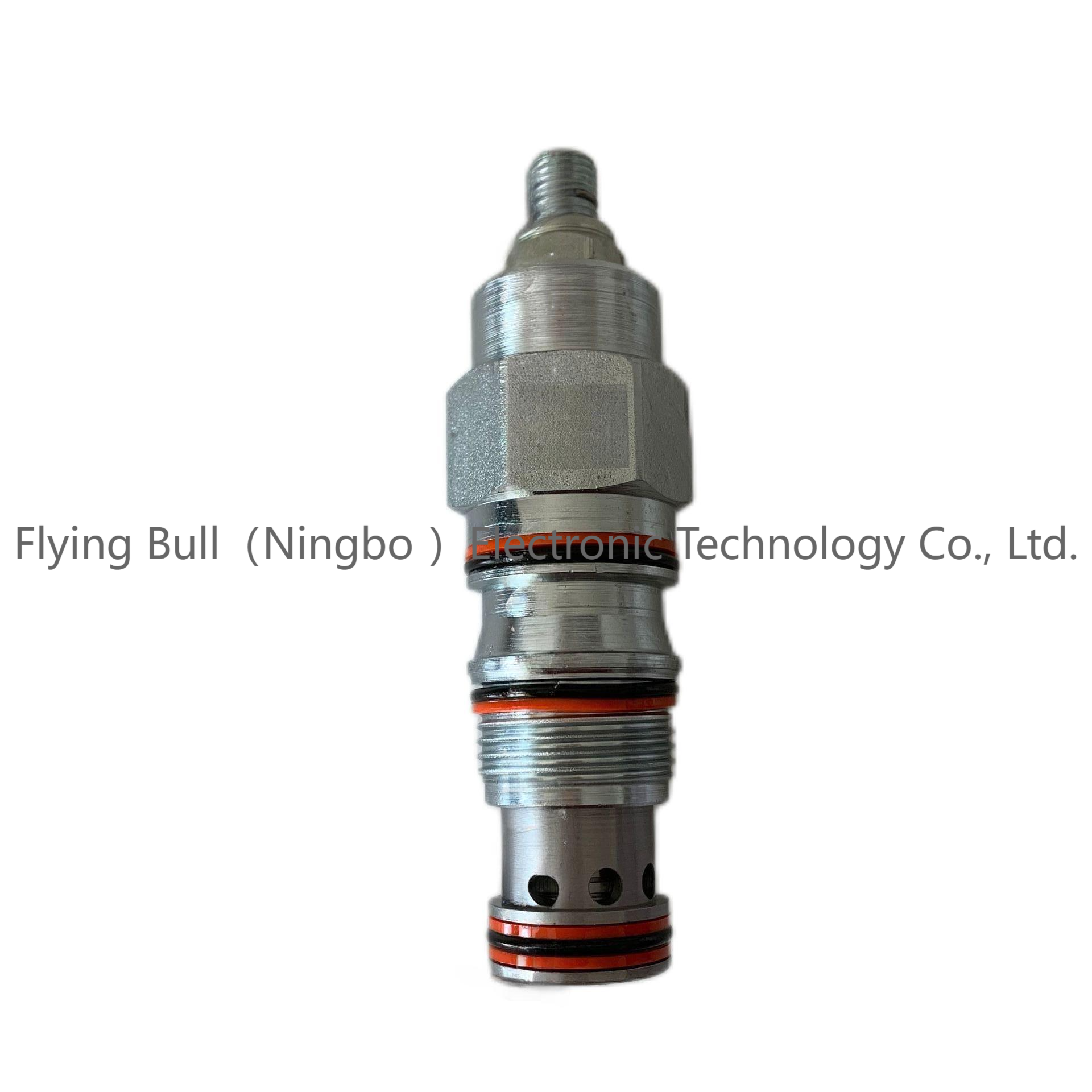
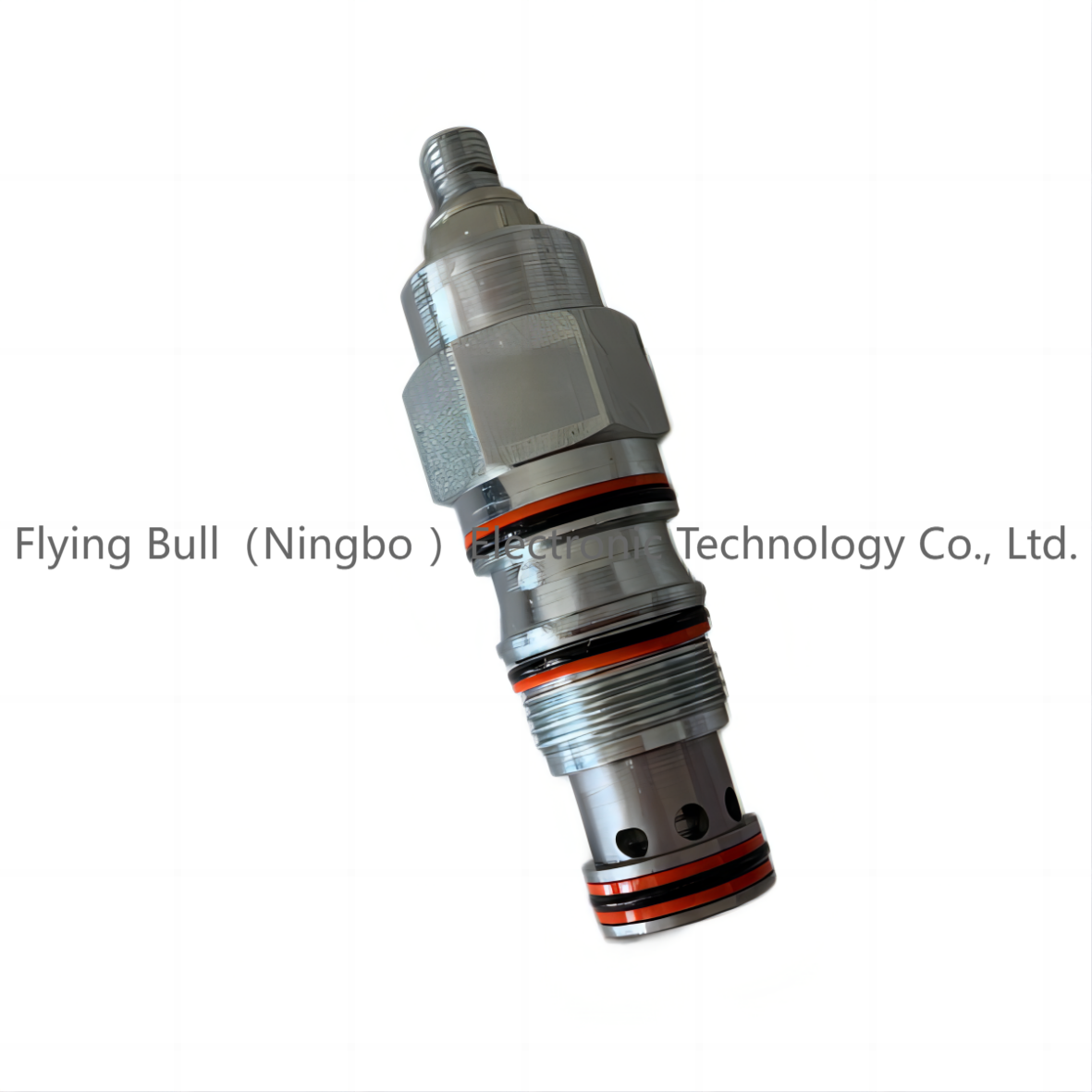
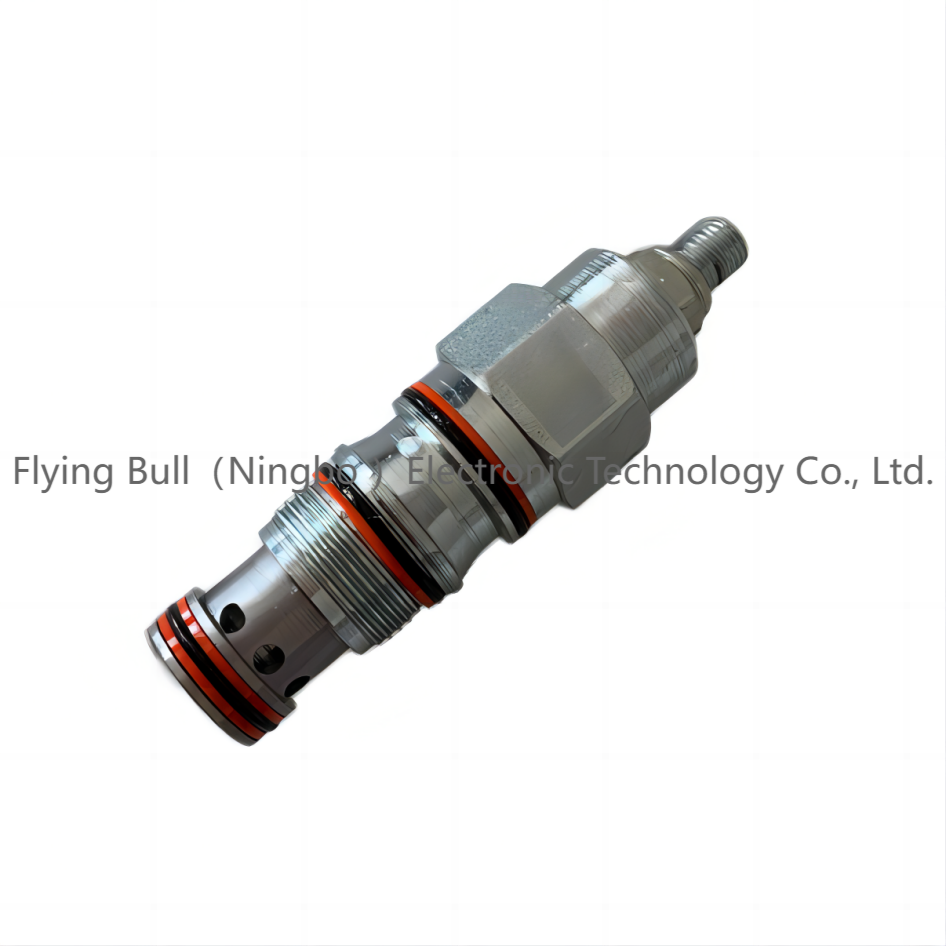
Company details

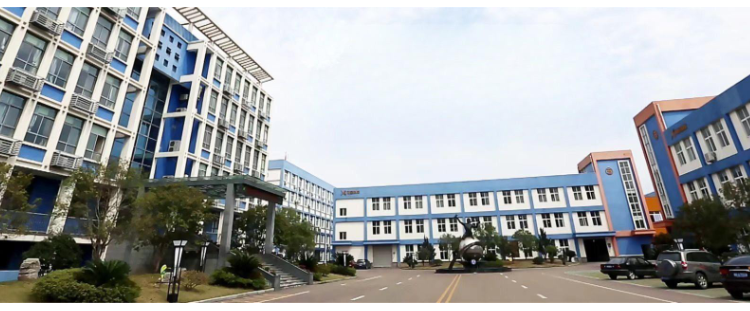
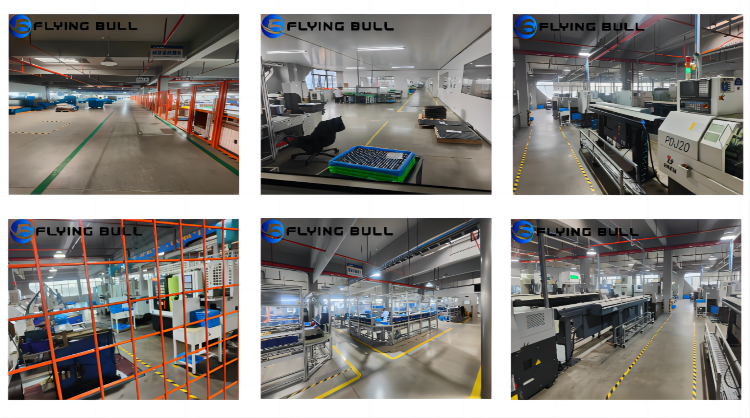
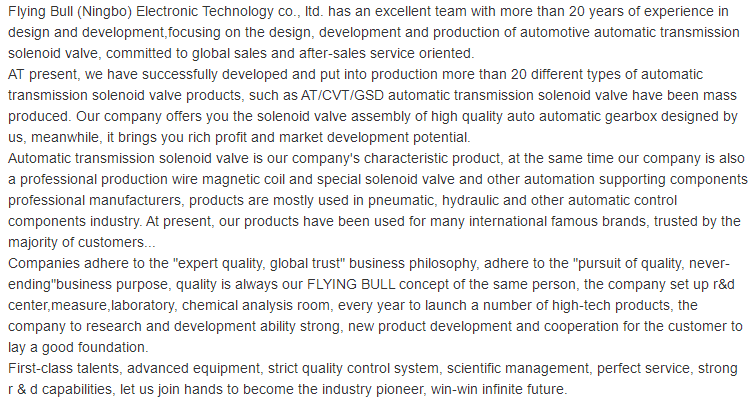
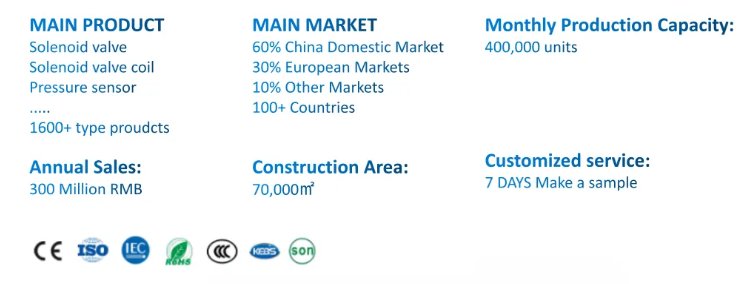
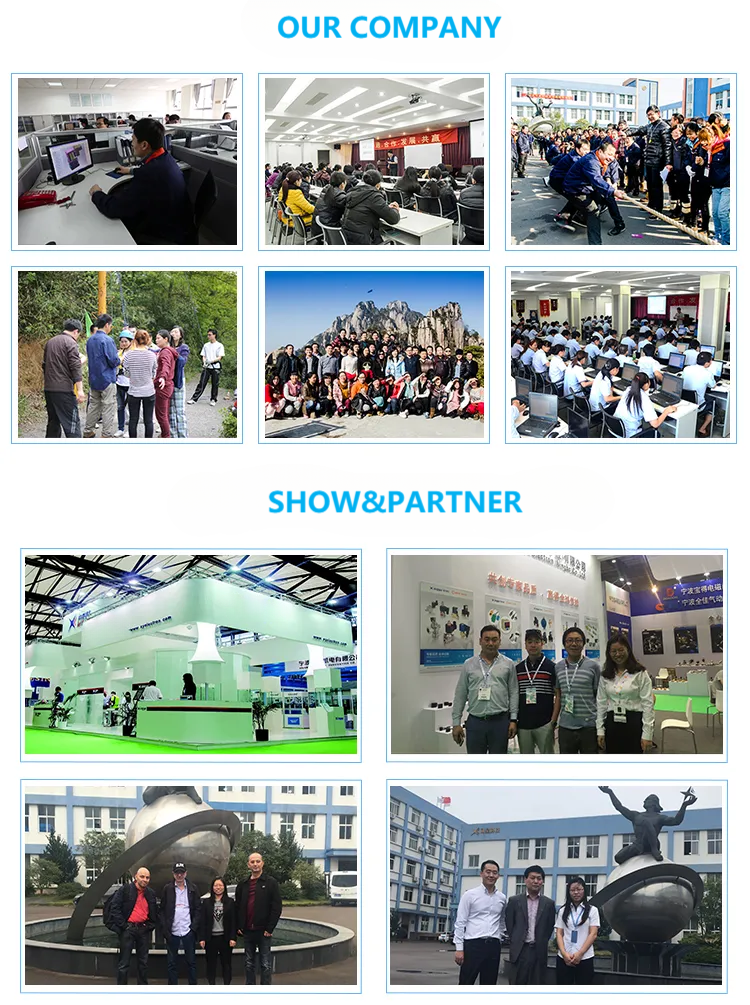
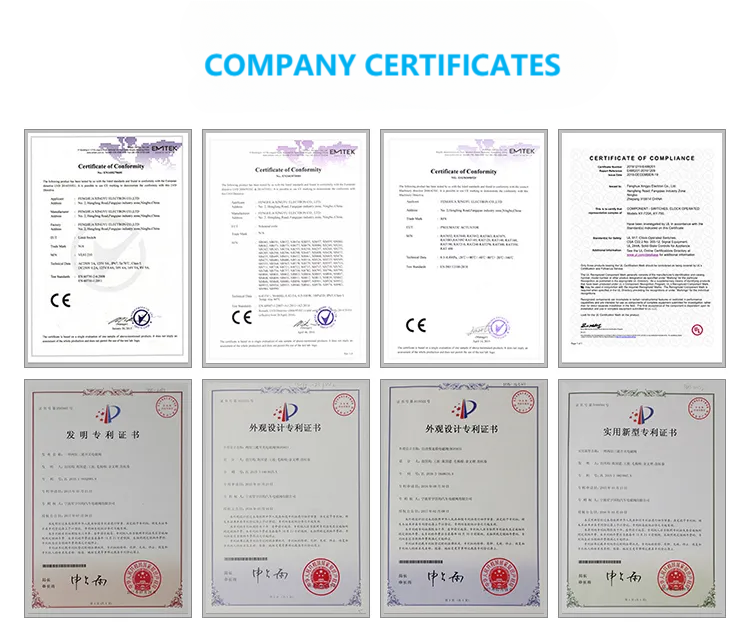
Company advantage

Transportation
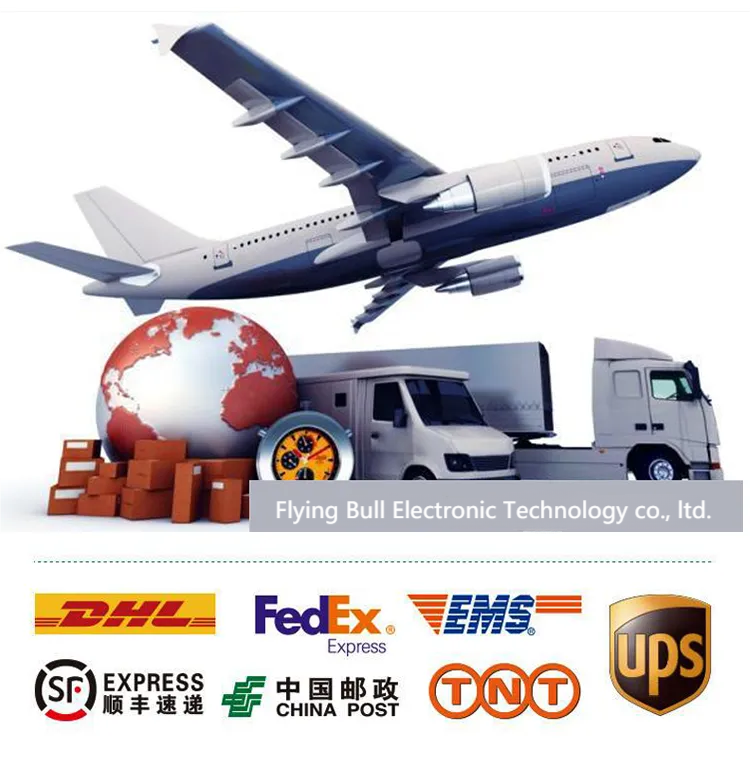
FAQ
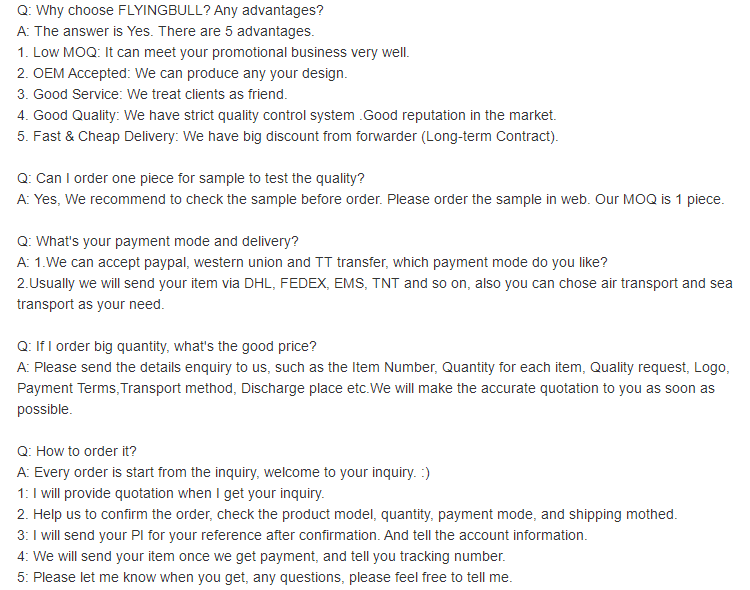