Excavator accessories John Deere AT310587 proportional solenoid valve excavator
Details
Sealing material:Direct machining of valve body
Pressure environment:ordinary pressure
Temperature environment:one
Optional accessories:valve body
Type of drive:power-driven
Applicable medium:petroleum products
Points for attention
What is the role of the directional valve and the pilot valve in series of the directional valve of the hydraulic proportional valve
The oil inlet and outlet control of the traditional reversing valve is carried out through a spool, and the corresponding relationship between the two oil port listening openings has been determined as early as the design and processing of the spool, and it is impossible to modify during use, so that the flow or pressure through the two oil ports can not be independently controlled and do not affect each other.
With the decrease of the cost of microprocessing controller and sensor components and the continuous improvement of control technology, the dual-spool control technology has been applied in the field of construction machinery. The British Utronics company uses its own technology and patent advantages to develop a double-core multi-way reversing valve, which has been widely used in JCB, Deere, DAWOO, CASE and other companies of excavators, trucks, loaders and excavating loaders and other products. In order to meet the functional requirements of hydraulic system for Chinese construction machinery products. With the continuous improvement of stability and automation control, Utronics products have entered the Chinese market in a timely manner, and have initially completed the commissioning of Xiagong (5t) loaders and Janyang (8t) excavators and entered the test stage.
1. Defects of traditional single-spool directional valve
The hydraulic system composed of the traditional single-spool directional valve is difficult to reasonably solve the contradiction between the following functions and control:
(1) In order to improve system stability and reduce the impact of load changes on speed, the hydraulic system is designed to either sacrifice some of the functions we want to achieve, or add additional hydraulic components, such as speed control valves, pressure control valves, etc. AI improves the stability of the system by increasing damping and improving the speed stiffness of the system. But the addition of such components will reduce efficiency and waste energy; It will also reduce the reliability of the entire system and increase the cost.
Product specification
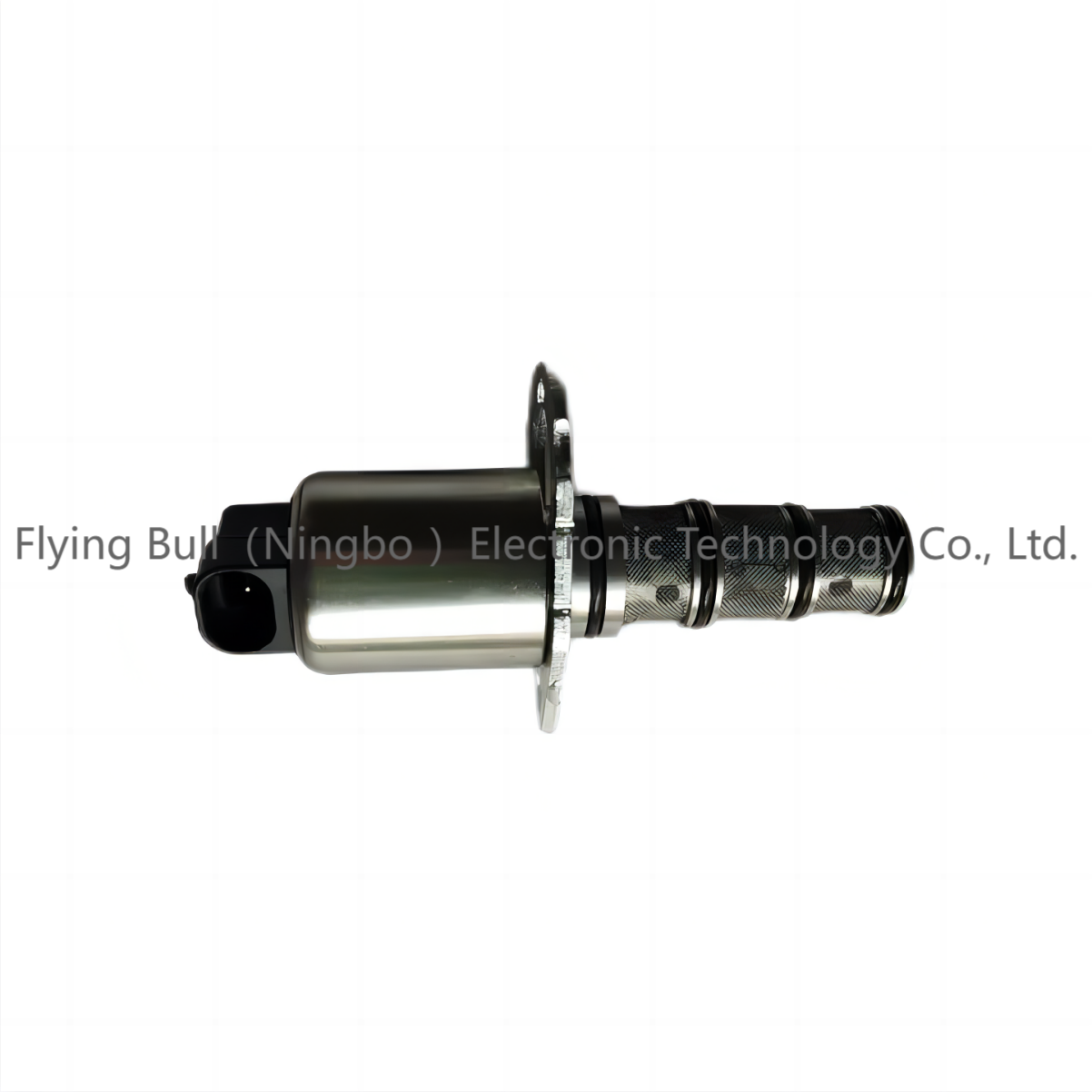
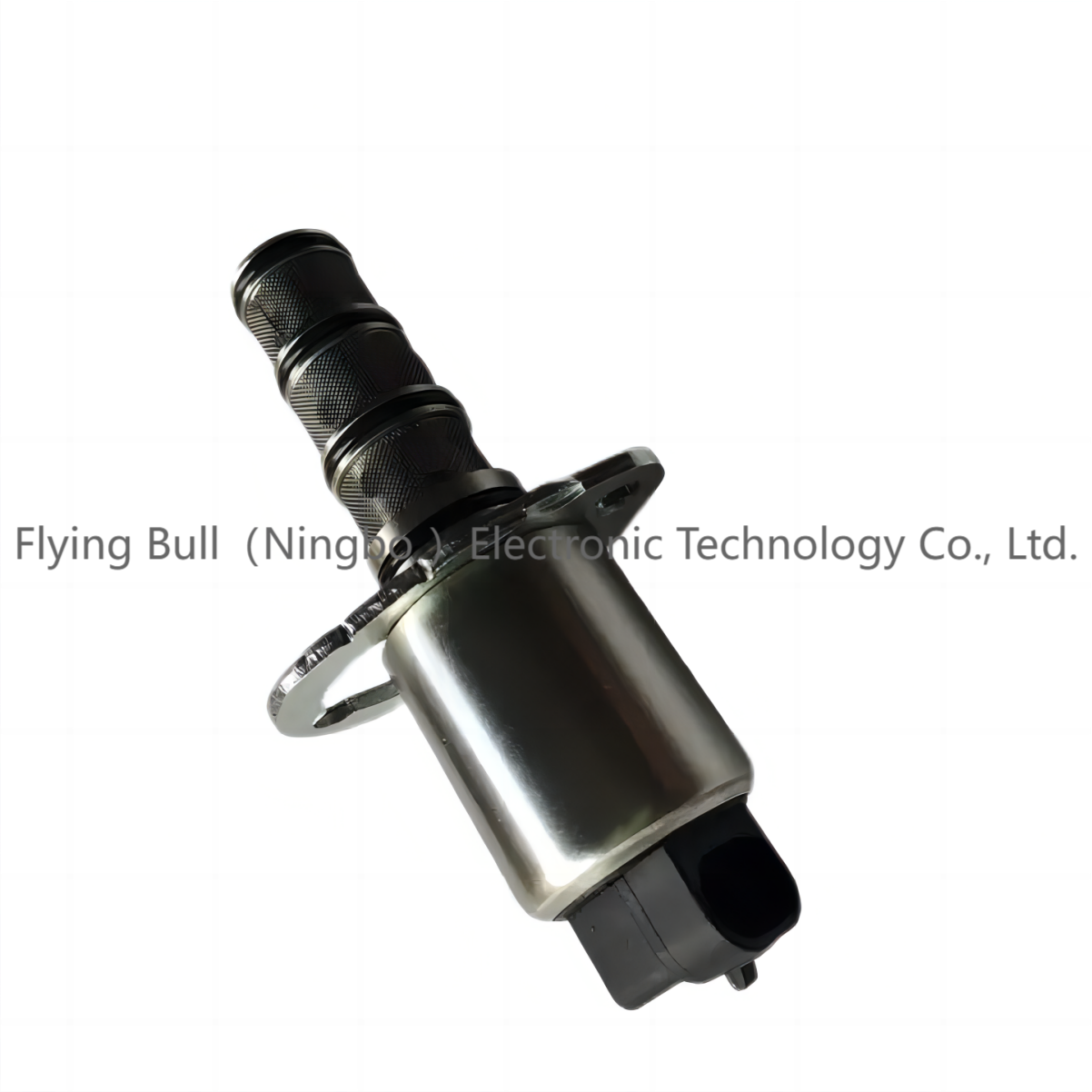
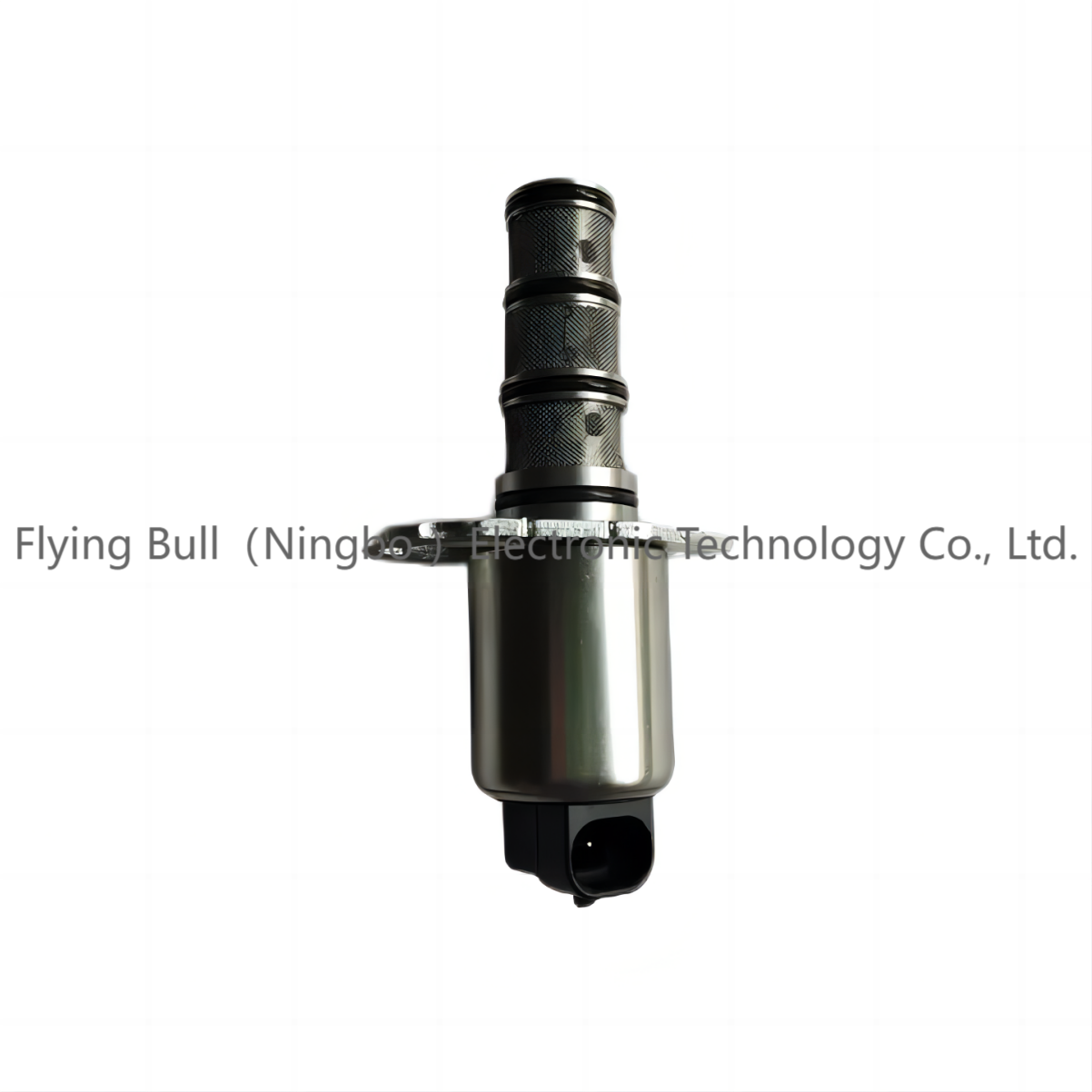
Company details

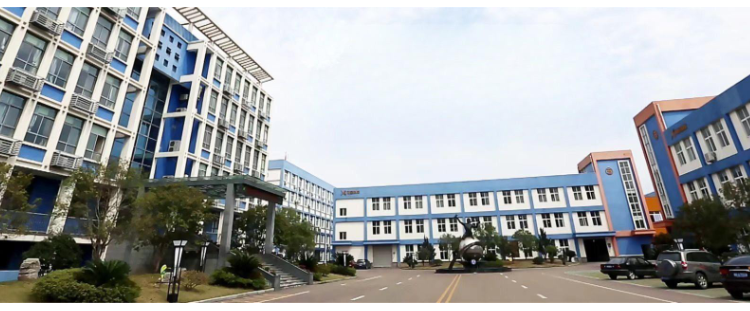
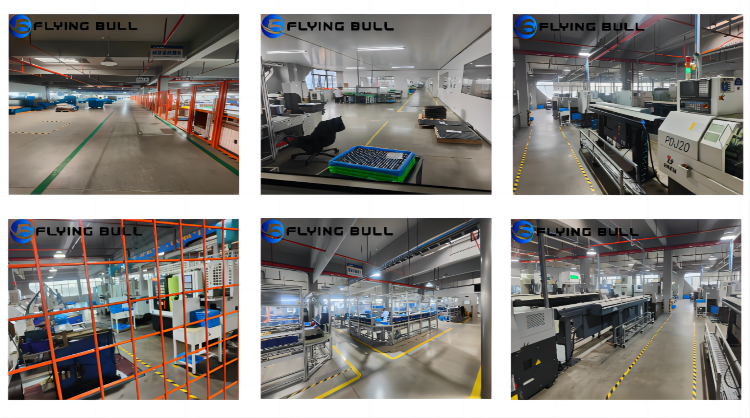
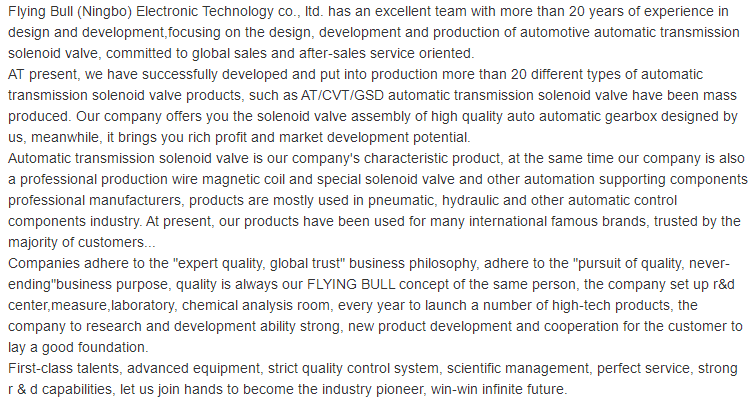
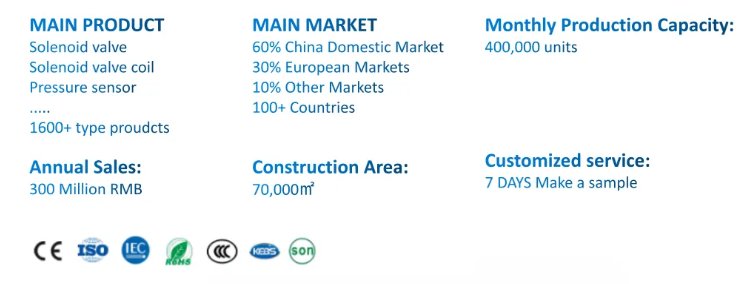
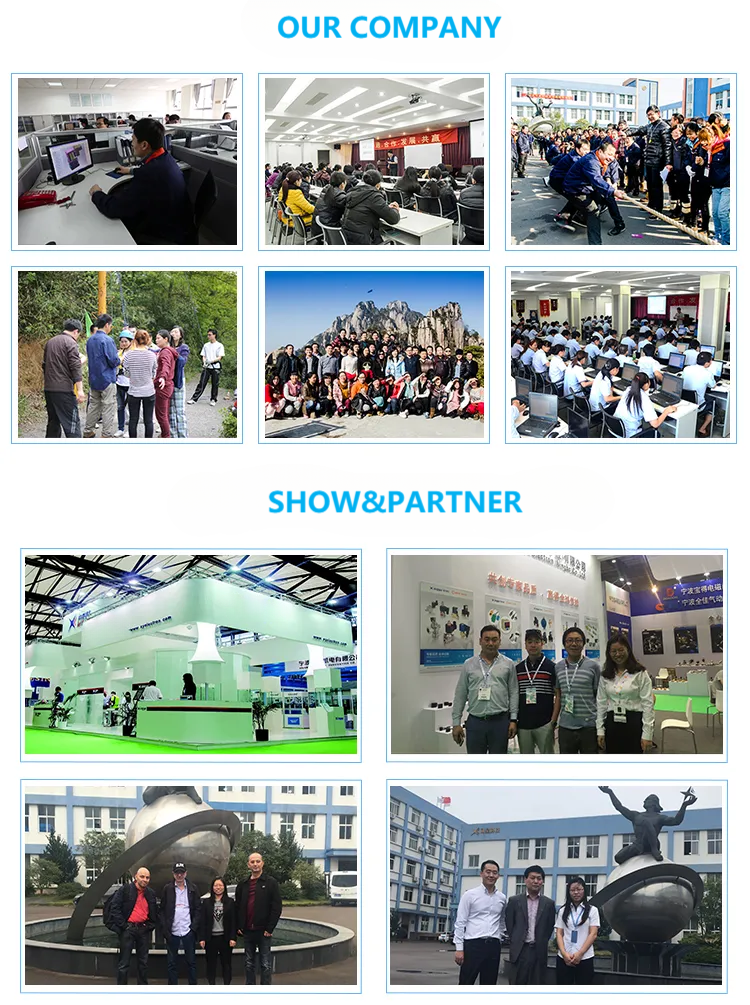
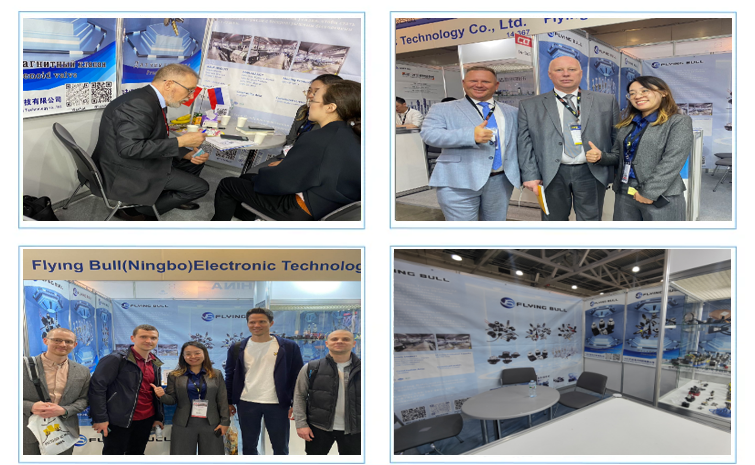
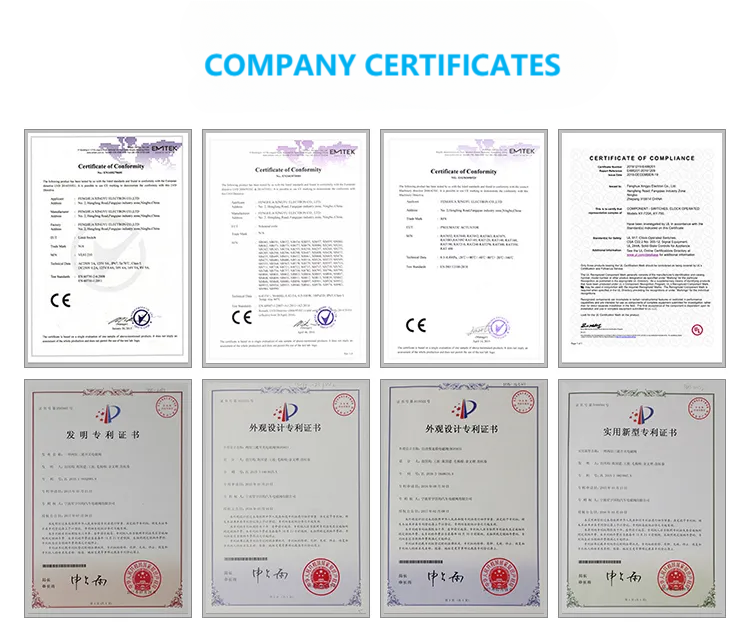
Company advantage

Transportation
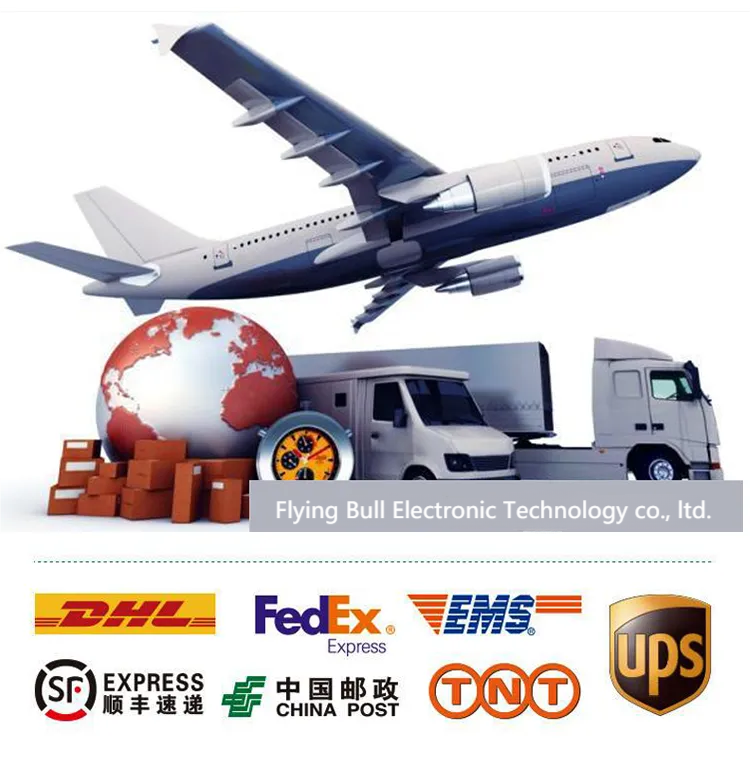
FAQ
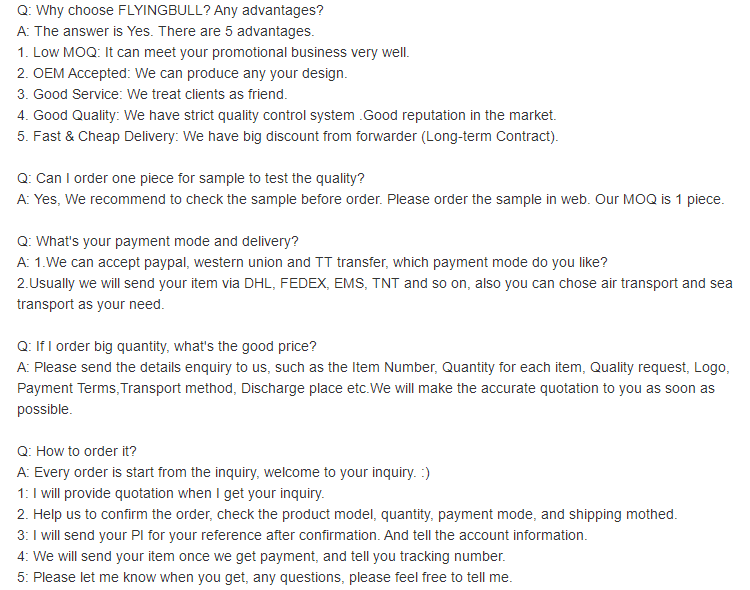