Suitable for Cummins vehicle pressure sensor 4327017
Product introduction
1. Shock and vibration
Shock and vibration can cause many problems, such as shell depression, broken wire, broken circuit board, signal error, intermittent failure and shortened life. In order to avoid the shock and vibration in the assembly process, OEM manufacturers should first consider this potential problem in the designer and then take measures to eliminate it. The simplest method is to install the sensor as far away from the obvious shock and vibration sources as possible. Another feasible solution is to use vibro-impact isolators, depending on the installation method.
2. Overvoltage
Once the OEM has completed the machine assembly, it should be careful to avoid the overvoltage problem, whether in its own manufacturing site or at the end user's place. There are many reasons for overvoltage, including water hammer effect, accidental heating of the system, voltage regulator failure and so on. If the pressure value occasionally reaches the upper limit of withstand voltage, the pressure sensor can still bear and will return to its original state. However, when the pressure reaches the bursting pressure, it will lead to the rupture of the sensor diaphragm or shell, thus causing leakage. The pressure value between the upper limit of withstand voltage and the rupture pressure may cause permanent deformation of the diaphragm, thus causing output drift. In order to avoid overvoltage, OEM engineers must understand the dynamic performance of the system and the limit of the sensor. When designing, they need to master the interrelationships among system components such as pumps, control valves, balance valves, check valves, pressure switches, motors, compressors and storage tanks.
The methods of pressure detection and checklist are: supplying power to the sensor, blowing the air hole of the pressure sensor with the mouth, and detecting the voltage change at the output end of the sensor with the voltage range of the multimeter. If the relative sensitivity of the pressure sensor is large, this change will be obvious. If it doesn't change at all, you need to use a pneumatic source to apply pressure. By the above method, the condition of a sensor can be basically detected. If accurate detection is needed, it is necessary to apply pressure to the sensor with a standard pressure source, and calibrate the sensor according to the magnitude of the pressure and the variation of the output signal. And if conditions permit, the temperature of relevant parameters is detected.
Product picture
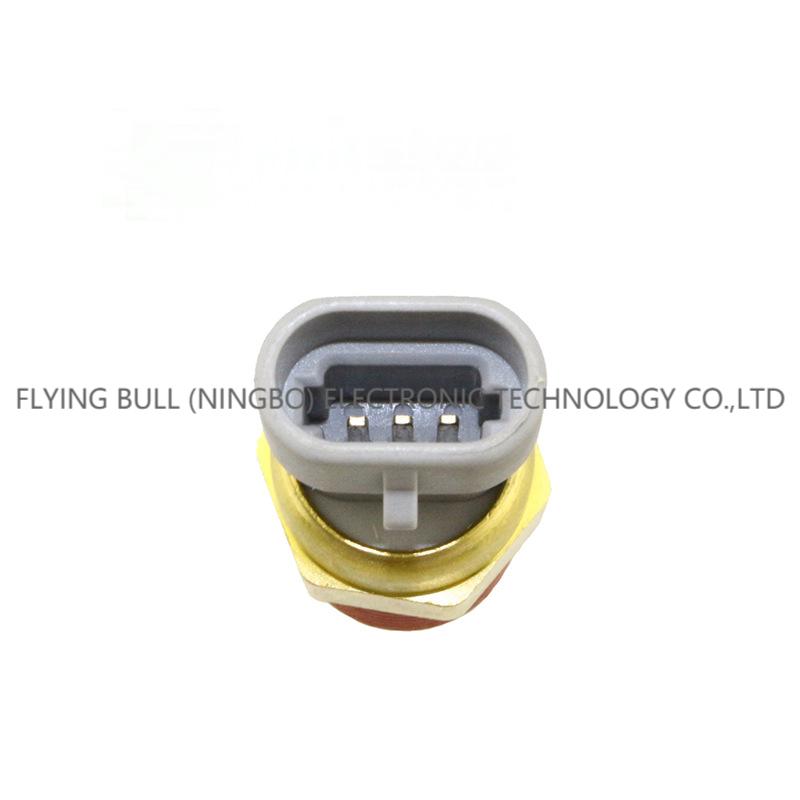
Company details

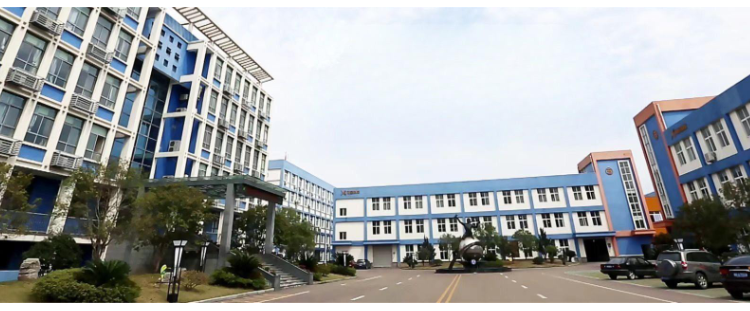
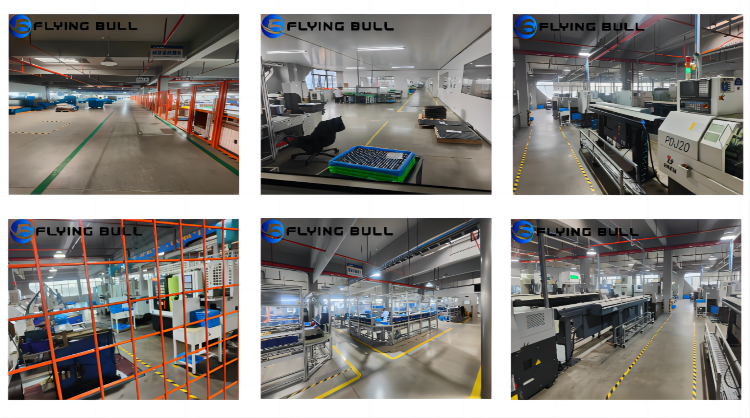
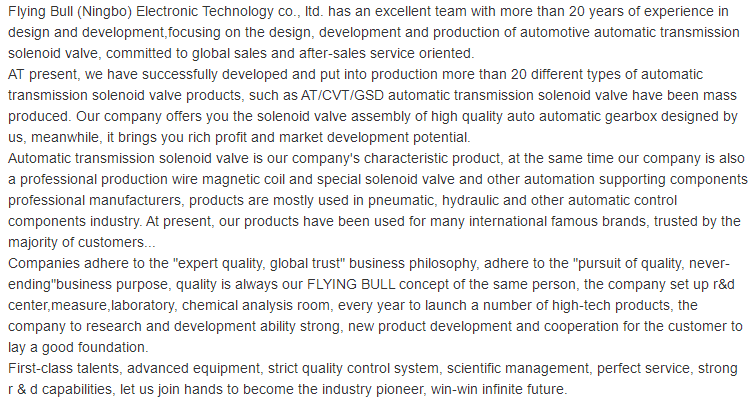
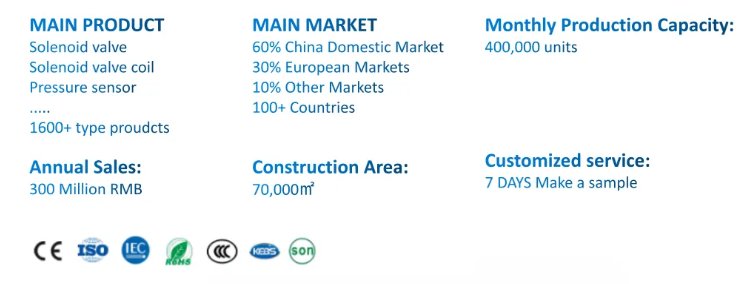
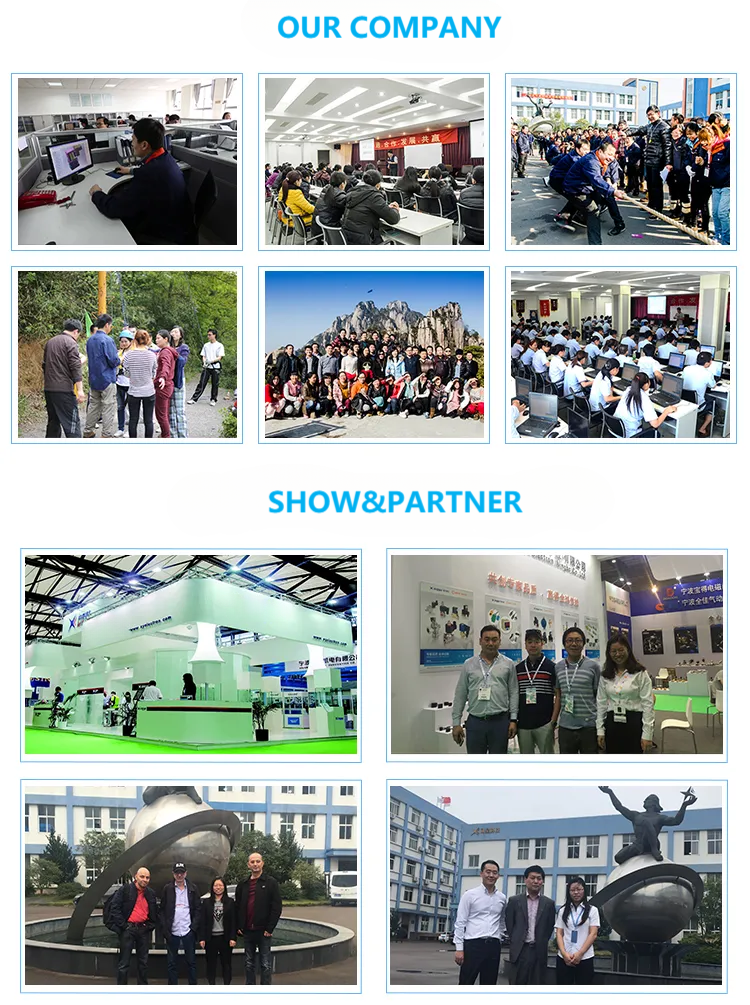
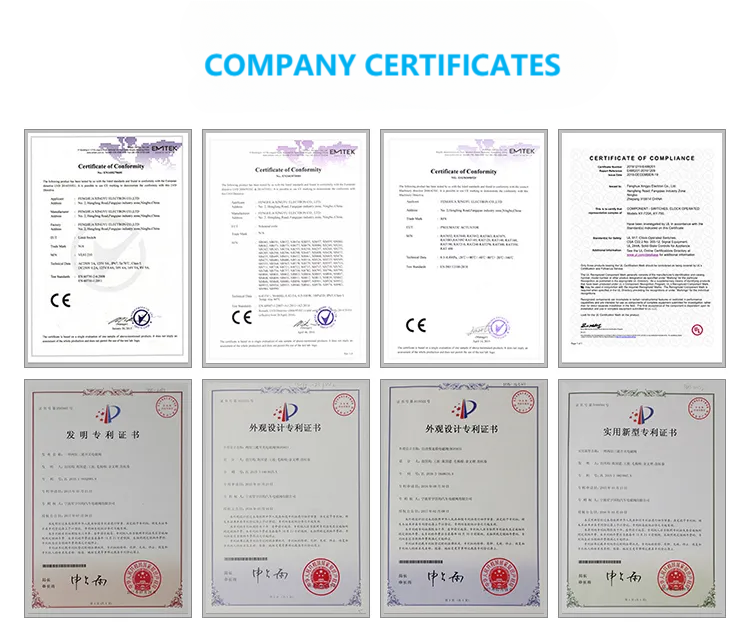
Company advantage
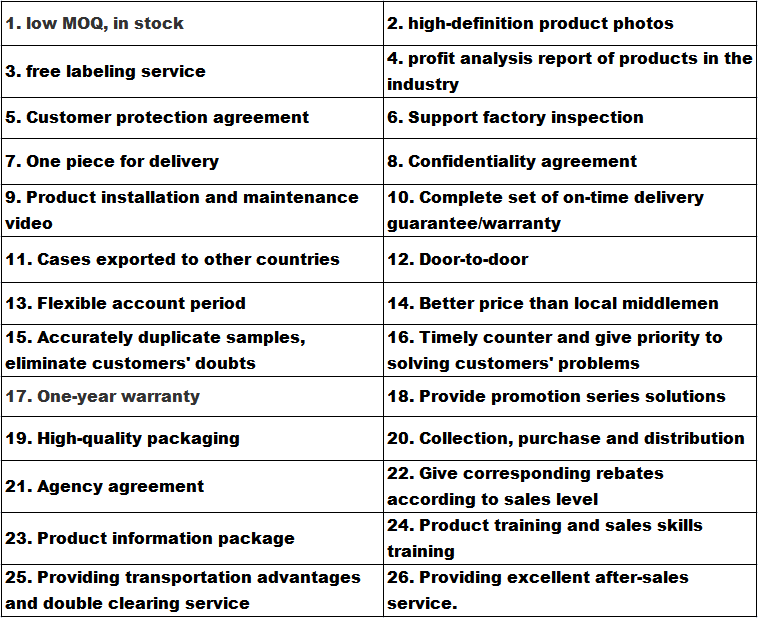
Transportation
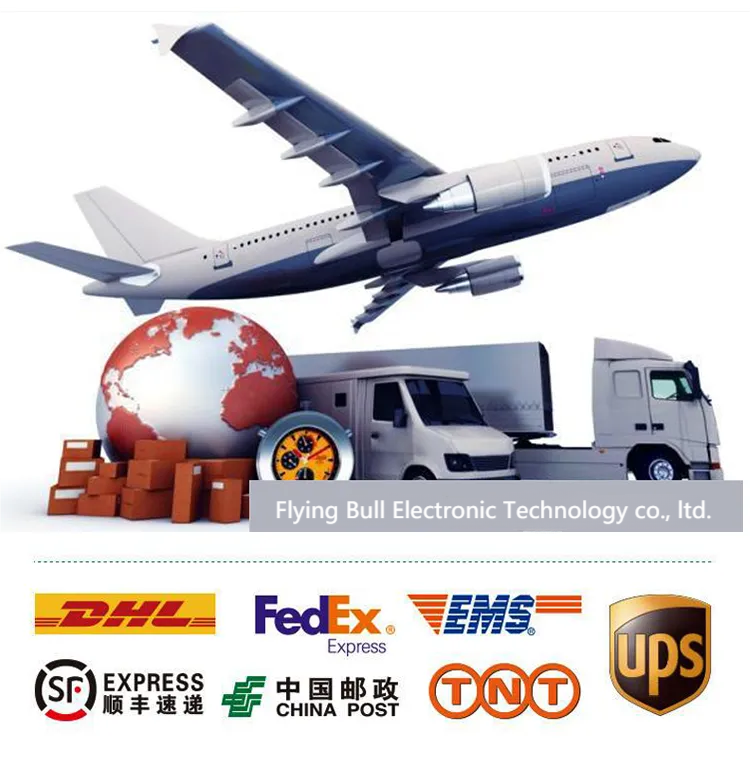
FAQ
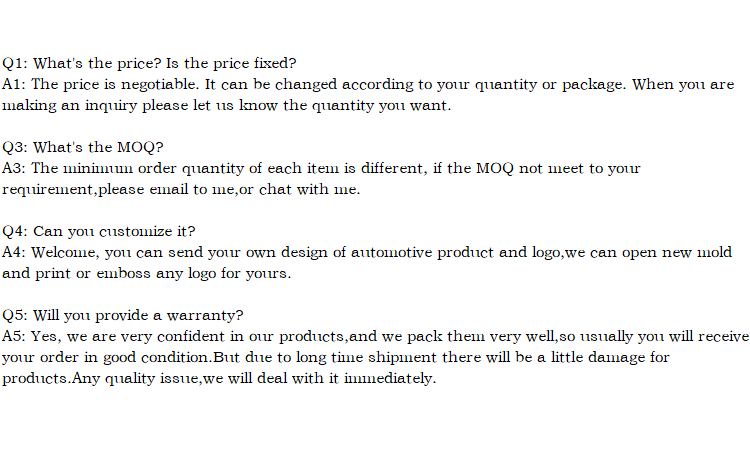